Click here to get this post in PDF
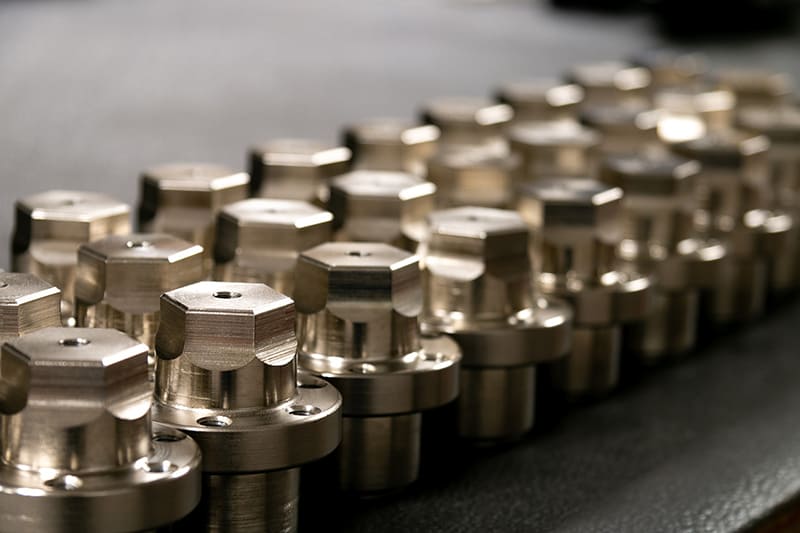
Regardless of whether or not your business deals with metal directly, it will often be a part of your business operation, sometimes without you even thinking about it. It could be as simple as the metal gates to your factory or office building, the metal elements of your company cars, or if you deal directly in manufacturing parts for other businesses.
While there are lots of incredible things that can be done with metal, it also has drawbacks. From a business point of view, these issues can cost money to resolve, money which could be better spent on other areas of the business. Furthermore, if you’re manufacturing parts made of metal, if the finished product is of poor quality, this could lead to future business loss. To avoid these issues down the line, there are several steps businesses can take to protect metal elements.
One of the most common forms of pre-treatment is phosphate coating. This process involves either dipping metal elements into a solution or spraying the parts with a liquid. As a result, the metal parts receive a protective coating with several benefits. Reducing corrosion is one of the main benefits of phosphate coating; however, it can also improve paint adhesion to the metal while, in other cases, improving the lubrication. Depending on the business and its needs, these benefits could produce better products that would serve customers longer due to reduced corrosion. Businesses that can demonstrate their products are high quality and are worth investing in generally have prolonged success in their industry.
For other businesses, working with metals may be about finding a way to reuse what they already have. As mentioned earlier, this could be as simple as improving the metal gates on the front of a factory. While the first thought may be to replace the gates, several steps can be taken to improve the existing ones and get them looking great without spending the money on installing brand-new ones. Industrial coating Sydney has provided exceptional protective coatings and abrasive blasting solutions covering all your requirements.
Choosing the right abrasives for blasting depends on several factors, including the type of surface being blasted, the required finish, and the equipment used. High-performance abrasives are better because they produce less dust, can do the job faster, use less abrasive material, and allow for better work visibility.
Businesses can utilise shot blasting, which strips any old paint and rust away from a metal surface using an aggressive technique involving chilled iron grit, to create a high-quality finish. After a piece of metal has been through a shot blasting process, the surface of the metal is in a much better condition to receive a new coat of paint. Because the surface has been cleaned thoroughly, the applied paint can last longer while looking better.
If businesses need to paint metal parts, one system which has shown to be beneficial is powder coating. Not only does this produce a high-quality and long-lasting finish, but the process also has financial benefits. Because powder coating uses dry paint powder, any excess powder which does not adhere to the metal can be collected and reused. However, this is only applicable if the paint powder is not mixed with another colour. Compared to wet spray painting and other traditional methods of painting, powder coating produces significantly less waste, making it more financially beneficial. Furthermore, it is more environmentally friendly, emitting no volatile organic compounds into the atmosphere. Check out RAMSEIER KOATINGS for more details of their powder coating systems
Overall, by understanding the benefits of metal pre-treatment, cleaning, and powder coating, businesses can not only improve the quality and longevity of their products but also save money.
You may also like:
The Role of Functional Industrial Coatings in Enhancing Equipment Longevity
How to Source Products from China? 6 Pro Tips for E-commerce Sellers
Image source: Pixabay.com
[…] You may also like: The benefits to businesses of metal pre-treatment and powder coating […]