Click here to get this post in PDF
A manufacturing or production problem can be a nightmare for a small business owner. If something goes wrong during the manufacturing process, it can delay your shipments. You may have to recall your products, and customers could file lawsuits against you.
Many people believe they have the best product globally, but if their manufacturing process is not up to par, it will all be worth nothing. A product can be a complete flop if it doesn’t satisfy the market’s needs. This article looks at some common manufacturing problems and how they can be avoided.
Tolerance Issues
Many factors can cause tolerance issues, including temperature changes, parts being assembled by hand, and machines being used for an extended period. Tolerance issues can also occur when there has been a change in personnel.
When tolerance issues occur, pieces often do not function correctly or fit with other parts properly. This problem occurs most frequently in mass production since there are so many different parts involved. When tolerance issues are discovered during the manufacturing process, it can lead to a massive loss of money and valuable time. The best way to avoid tolerance issues is to conduct thorough tests before a large-scale manufacturing process begins so that all of the details are taken care of before they go into production.
Equipment Failure
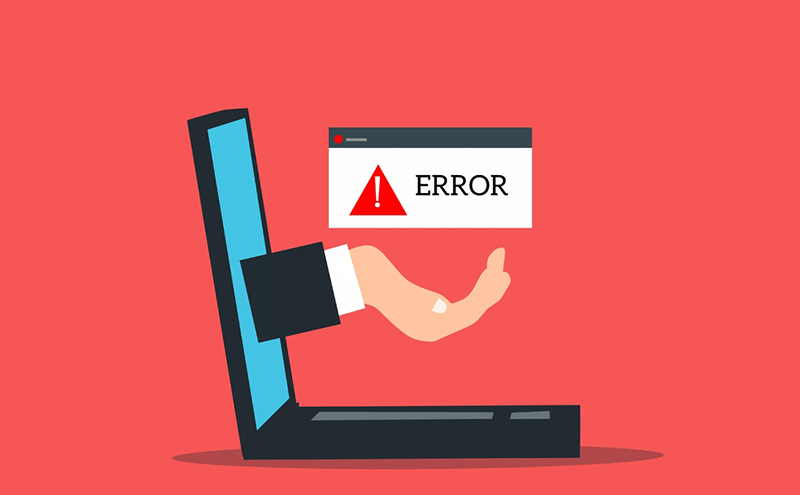
A critical aspect of any manufacturing business is the ability to produce quality products in a timely manner. If your factory cannot meet demand, you will not be able to make sales, and your reputation will suffer. At the same time, if you cannot produce at all due to non-working machinery, your business will be in trouble.
Most manufacturers face equipment failures at some point, which causes them to miss deadlines. This can be disruptive to your business and hurt your reputation with customers. You can do some things to help minimize the issues that arise with equipment breakdowns, like proper equipment handling and maintenance. Implementing solutions like those provided by MCA Connect can streamline your equipment management, thereby allowing you to deliver on time.
Example: Equipment Downtime Dilemmas
Extraction equipment plays a pivotal role in various manufacturing processes. Downtime due to equipment failure can result in significant setbacks. Implement a proactive maintenance schedule for your machinery, addressing potential issues before they lead to downtime. Regular equipment upgrades and investing in cutting-edge extraction equipment can also enhance efficiency and minimize disruptions.
Delay in Inspection
Many companies fail to meet their production deadlines because of the inspection process. The inspection process is not just a good practice in terms of quality control; it is also a legal requirement. By law, a QA professional must inspect each batch of products produced in the factory before the production run can be shipped out. Complex designs and high production volumes make it difficult to inspect every product at every stage. However, specific procedures can be adopted to ensure smooth production and timely delivery.
This issue is common among manufacturers and clients when they ship their products to retailers. The problem arises when the delay in inspection results in the expiration of dates in terms of quality standards. At that time, retailers reject your products because they have lost their original quality standards by the time they are inspected at the retailer’s end. This issue can be solved by taking a delivery inspection before shipping to be cleared from the client’s end to avoid this problem.
Poor Customer Communication
Poor communication with customers and suppliers can be a real problem for small businesses. Keep your communication channels open. Ensure you have multiple ways to reach your customers, including email and telephone. Also, make it easy for them to contact you. Provide your phone number or email address on forms and questionnaires, including a link to your website in all correspondence, and make sure you respond promptly. Here are some tips to bear in mind for effective communication:
- If using email, use plain text (avoid fancy fonts and graphics) so that it is more likely to be read.
- Create a folder in your email inbox specifically for communications with customers. Make sure you reply to emails within 24 hours or as soon as possible but no longer than 72 hours.
- Use a tracking system to keep track of inquiries and responses and when they were sent – this will help you if someone has not received a response.
- When communicating with suppliers, use the same principles – make sure that you keep multiple communications channels open and that the message is clear.
- If you are sending an important request or query, follow up by phone if there is no response within 24 hours.
Product Standards
The most important thing to know about product standards is that they are set by the customer, and the manufacturer must meet them. The customer has to specify what they want under these categories before purchasing your product. If you do not provide what they want, they will not buy your product. You want to ensure that you do not provide them with something different from what they expect. For example, if the customer wants four medium-sized t-shirts, you must provide them with four medium-sized t-shirts. You cannot give them four extra-large t-shirts even though you think that is better than four medium ones. Remember, it’s your job to guarantee that the product standard requirements are met. If you don’t ensure this, you will lose sales to other companies that can step up with their product standards.
Takeaway
When manufacturing products, it’s essential to be bluntly honest and open with your supplier. Don’t keep anything from them, be open, let them know the situation because you never know what inspired solution they will use to fix the problem.
You may also like: How to Increase Productivity in Your Manufacturing Firm