Click here to get this post in PDF
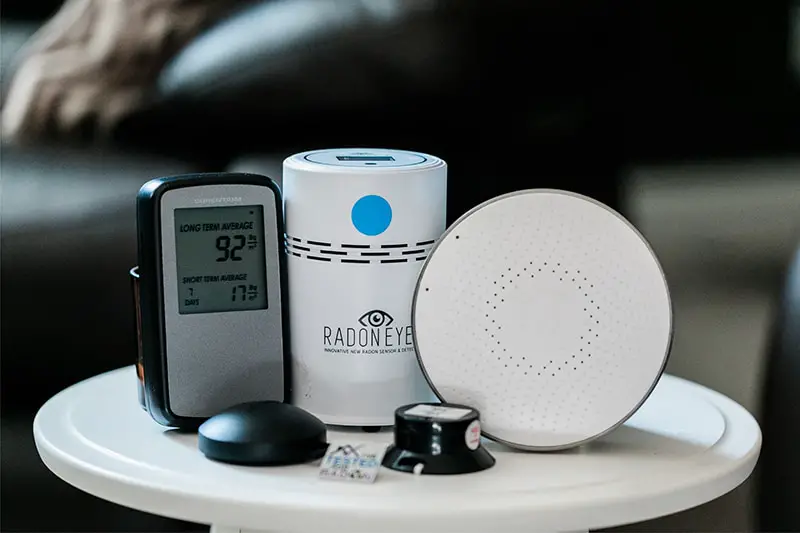
In the UK, it is a legal requirement and obligation for employers within certain sectors to undertake breathing air testing. These air-breathing checks ensure the safety of employees, clients and any other visitors to the building.
Samples should be tested every three months or more frequently, extra compressed breathing air quality tests should be carried out if there have been concerns or change in the process of production.
Why Is Compressed Breathing Air Testing Important?
HSE guidelines stipulate that these tests should be carried as per each building’s risk assessment every three months. These tests may be required to be completed more often if the levels of air cannot be assured.
In the case of breathing-air compressors that are mobile, COSHH states the air should be tested every time the unit is moved, or upon the change of prevailing wind conditions.
Without these tests, individuals who are exposed to this air could be at risk of breathing in harmful particles that could lead to both long- and short-term health problems. If an employee should fall victim to inadequate air testing, the employer will be liable for any repercussions including financially compensating the victim.
The most common issue within employees who have worked in poor conditions is lung problems and breathing issues, various forms of cancer and in a worst-case scenario, death.
What Are Employer Responsibilities?
In every business premises, employees are legally responsible for the safety of their employees and in many sectors, they are also required to follow the Control of Substances Hazardous to Health Regulations (2002).
These industries include any environment where there is insufficient oxygen, dangerous gasses and/or vapours (such as carbon monoxide). Other environments include areas with hazardous airborne particles such as asbestos, dust, fungal spores and bacteria or any liquid particles that could be harmful such as spray paint oil or pesticides.
Every person who will be operating breathing air equipment must be fully trained to industry standards and supervised while operating these machines.
The correct PPE must be provided by the employer and be suitable for the wearer, this includes facepieces that correctly fit various face shapes and sizes that can accommodate facial hair and glasses.
What Tests Must Be Conducted?
The minimum requirements any breathing air can be is stipulated in BS EN 12021. This requires that all machinery and equipment for compressed air for breathing cannot possess any contaminants where the concentration levels could be toxic or harmful.
All contaminants should always be kept as low as possible in any industry and should always be far below the national exposure limit. This must be less than 1/10 of the national 8-hour exposure limit.
Oil, dust and other particles can develop over time in a compressor and lead to machine breakdown and other failures. This is why in breathing air quality it is so essential that the air is regularly checked and maintained to remain as clear as possible to avoid any contamination.
Particularly if air compressors are moved around the building, they should be checked regularly and maintained.
These tests don’t always have to be completed by third parties, they can be conducted by those within the business, providing they have been given the right training to do so. This can be in the form of colour-change tubes, on-line gas testers or by collecting samples on-site and sending to external test centres.
Many businesses fail testing from forgetting one simple thing, the filters. The main filters within air compressors are there to collect particles or gases and vapours. Although very effective, they do not last forever. Checking these regularly and changing as per each manufacturer’s guidelines will help to prevent poor test results.
Keep A Paper Trail
Records of all testing and their results should be kept in a safe and secure location. Paper copies can be good, but these can easily go missing, storing these on external servers to ensure complete security will mean businesses are always covered should they be asked to produce these.
These records must be kept for a minimum period of five years. If businesses fail to do so, should any claim be made against the company regarding poor air and they can not prove the right testing was in place and the results were satisfactory, there could be serious implications in a court of law.
Importance of Air Compressors in Any Business
Every employer has a legal and moral duty to the staff members, clean air is a right for anyone in any industry, and those who pose more of risk need to take extra care wherever possible. All air compressors must be fully checked and maintained as frequently as possible as at least once every three months, alongside these breathing air tests.
Image Source: Pixabay.com