Click here to get this post in PDF
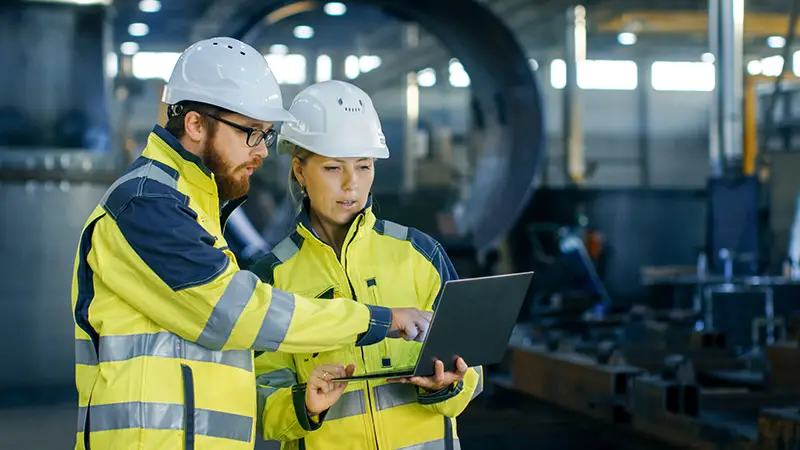
Many small businesses have faced hardship this year due to COVID-19. A survey conducted at the beginning of lockdown by the National Association of Manufacturers revealed that nearly 80% of manufacturers were expecting the pandemic to have a financial impact on their business.
Manufacturing is a fundamental aspect of many small businesses that produce items such as furniture, clothing, jewellery, or electrical items. To help get back on track after lockdown and continuously see profits increase in the future, read on to discover four money-saving tactics you can implement into your business strategy.
Invest in modern equipment
Incorporating advanced technology into the manufacturing process will increase the efficiency of your production, allowing you to boost profits. Whereas using outdated machinery can cause poor results, require more time to complete the task, and use more energy to function.
Stud welding, which entails attaching fastenings to metal sheets, is a popular form of welding commonly used across the manufacturing industry. The UK’s leading designer, manufacturer, and supplier of stud welding equipment, Taylor Studwelding, provides machinery that can weld up to 60 studs per minute.
If you use manufacturing equipment regularly, you’ll save money in the long run by purchasing in-house machinery instead of continually paying rental fees.
Motivate staff members
When employees feel disengaged with their job, it’ll show in the quality and amount of work they produce. If it takes them more time to manufacture the goods, it’ll cost you more than is necessary.
A previous survey by Salary.com found that 94% of employees within the engineering, design and construction industry wasted time daily. Nearly a third of the overall respondents wasted roughly one hour each day.
To enhance productivity, conduct thorough training sessions on how your employees can operate more efficiently and offer incentives to encourage staff to reach any set targets.
Ensure all the manufacturing duties are well-matched to suit your worker’s skill sets to see the best results from everyone involved. Don’t encourage multi-tasking either as splitting focus into two jobs is often unproductive and unsuccessful.
Outsource To Cheaper Manufacturers
Bringing labor costs down can be pretty tough, but if you find the right manufacturers you can outsource some work to them which is usually cheaper than having to hire more staff. You can also lower your costs by flipping from one company you outsource to, to a cheaper one. Always be on the lookout and make sure you get quotes in as often as you can. For example, if you’re looking for a 3D printing service you need to make sure you find one that can handle the volume you have in mind and one that also uses the right materials. You don’t want to drop in quality, so it’s all about forging those long-lasting relationships with other manufacturing companies. If you can outsource to someone who offers you the same quality for less, you’re going to save money. It doesn’t matter if you’re looking for 3D printing or plastic production. Pick up the phone and start looking.
Minimise errors
Manufacturing mistakes can waste materials and result in needlessly excessive use of stock. It also wastes time if errors result in workers re-doing the task.
If any blunders went unnoticed before the goods reached the market, you might have to recall the defective products and pay to retrieve and replace them. Recalls can hinder a business’s reputation and financial profitability too.
Automated machinery reduces this possibility by providing accurate and efficient results. For aspects of the manufacturing process that can’t be automated, hire experienced and reliable staff that you can trust to complete the job correctly.
Cutting Costs – 5 Easy Ways Your Small Business Can Save Money
Material expenses
If you’ve used the same material supplier for a long time, research whether there are any cheaper options available that won’t compromise the material’s quality. If you want to maintain a relationship with your current supplier, give them the opportunity to match their competitor’s prices.
You could sell any excess material leftover from projects to renovators and vendors as well. However, if this is a regular occurrence, consider ordering less stock to minimise the cost and wastage.
Enhancing the efficiency of your business’s manufacturing process will help reduce costs while also improving productivity and morale.
Image Source: Shutterstock.com