Click here to get this post in PDF
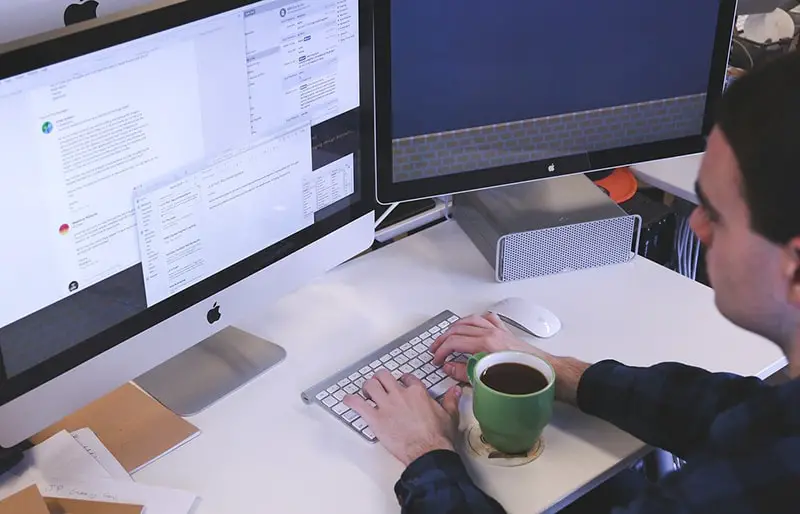
The following are a couple of steps you can take to reduce the risks involved in providing executives.
Mistakes in tying the board loosely can end up being extremely undesirable for the stability and growth of your business. Regardless of whether or not your company’s flexible chain is full of bungalows, it’s wise to move on, because the more mistakes you make, the less likely you are to be completely free from the chain. You can make a profit by increasing the benefits. Below are some of the steps you can take to reduce the risks involved in providing executives and improving the QualityOne.
Make your arrangements
By deciding to adjust to the latest developments, you choose better delivery, accommodation, and security. Mechanics reduce the risk of errors that are more common during manual cycles. This cycle is incredibly beneficial, while the solid establishment is based on robotization to make it more compatible with more suppliers who have grown up among peers.
Computerization provides you with an adaptable dashboard where you can track all basic information and cycles. In addition, it is worth the time because the chief does not have to investigate the seriousness of the task. Remember to protect your online information and physical safety efforts on the web. Restrict entry to important records and use the Secure Document Act to change or alter your information.
Do the proper documentation
No one can put too much pressure on the importance of proper documentation. Your flexible chain can be so restless and powerless that not all cycles in your framework are reported. Documents can be used to track stock, purchases, shipments, goods, and so on.
You can check in the event that you have received exactly the quantity and type of items you have requested. If something goes wrong, you can count a copy of your receipt from the provider so that any questions can be answered. Transportation notifications are an important function in communication regarding the movement of incomplete or damaged items.
Identify the most common mistakes
You can do a brief check to see where the most recognizable errors occur. Once you realize that, you can put time and cash aside by focusing on these issues and focusing on them through robotization. The two most widely recognized imperfections are being transferred to an inappropriate item and based on the way the price was determined. Purchase Order Approval (POA) can help the supplier verify the goods and their quantity before sending the product. Amazing work from a web quality administration framework like Viva Industries can help you eliminate such errors in the same way.
Guaranteed clear understanding
All methods of a flexible chain should be clearly visible to you. You should have the option to go through the whole cycle of who requested what, who is scheduled to access the message, who will receive the application, and a wide range of different things. Given that you have guaranteed to eliminate misunderstandings and that you have enough data on everything, you can differentiate between mistakes. In addition, you will know who to contact in such a case.
You may also like: How has Technology Boosted the Retail Supply Chain?
Image source: Pixabay.com